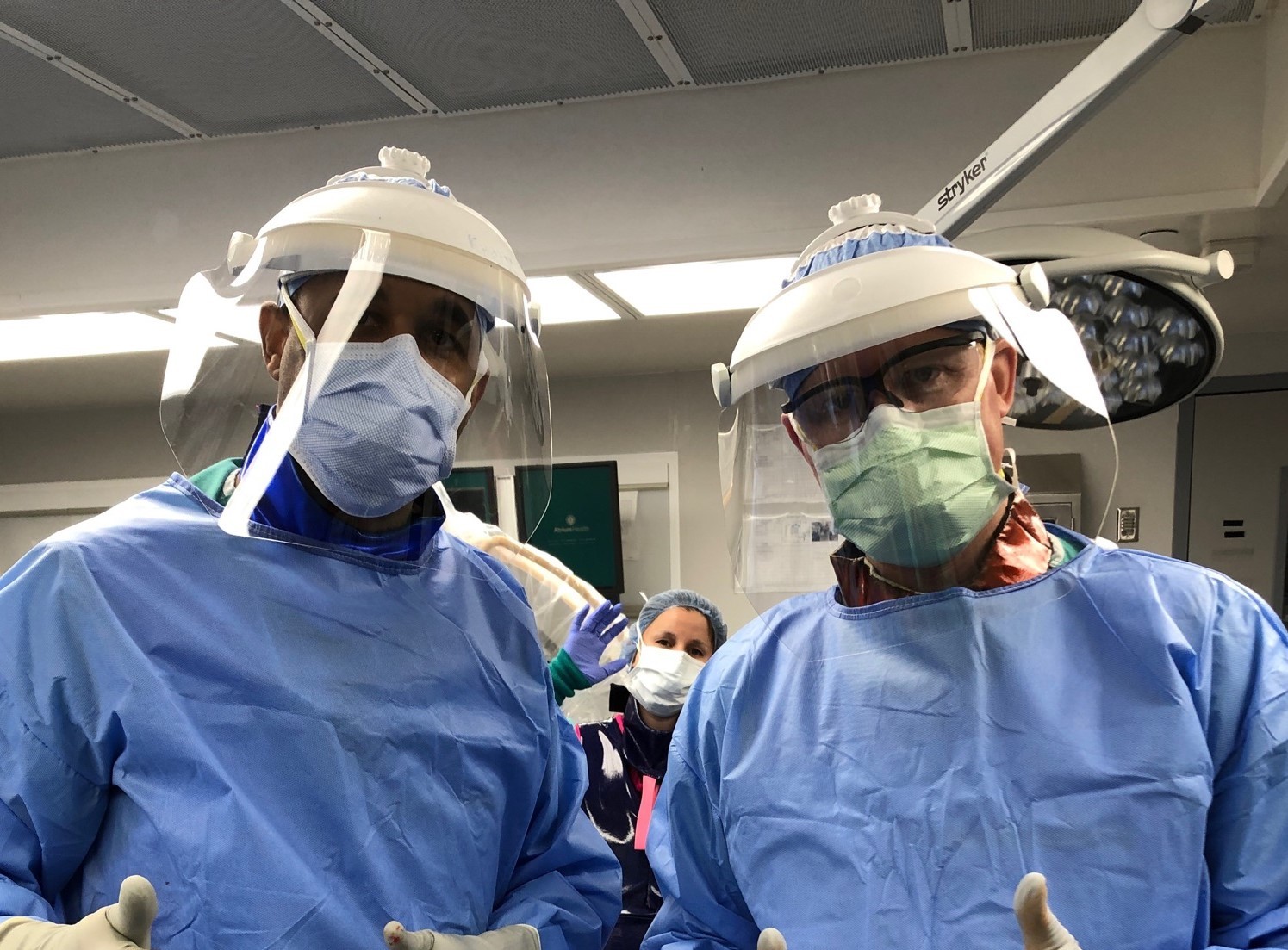
CONCORD, N.C. – 2020 has seen the world shift in ways many didn’t think possible. The novel coronavirus known as COVID-19 has affected the lives of nearly everyone across the globe. As people work together to flatten the curve and stop the pandemic from spreading, 12-time NASCAR Cup Series champions Hendrick Motorsports has teamed with a group of physicians at Charlotte-based Atrium Health, one of the nation’s leading healthcare organizations, to provide added protection to medical workers on the front lines of the crisis.
Utilizing 3D printers and laser cutters typically used for fielding four elite stock car teams, Hendrick Motorsports engineers Jim Wall, Tad Merriman and Mike Broskin, along with David Kapp, Jamie Lamb and Kevin Moler, have been working since the end of March to manufacture improvised personal protective equipment, or PPE, in the form of face shields.

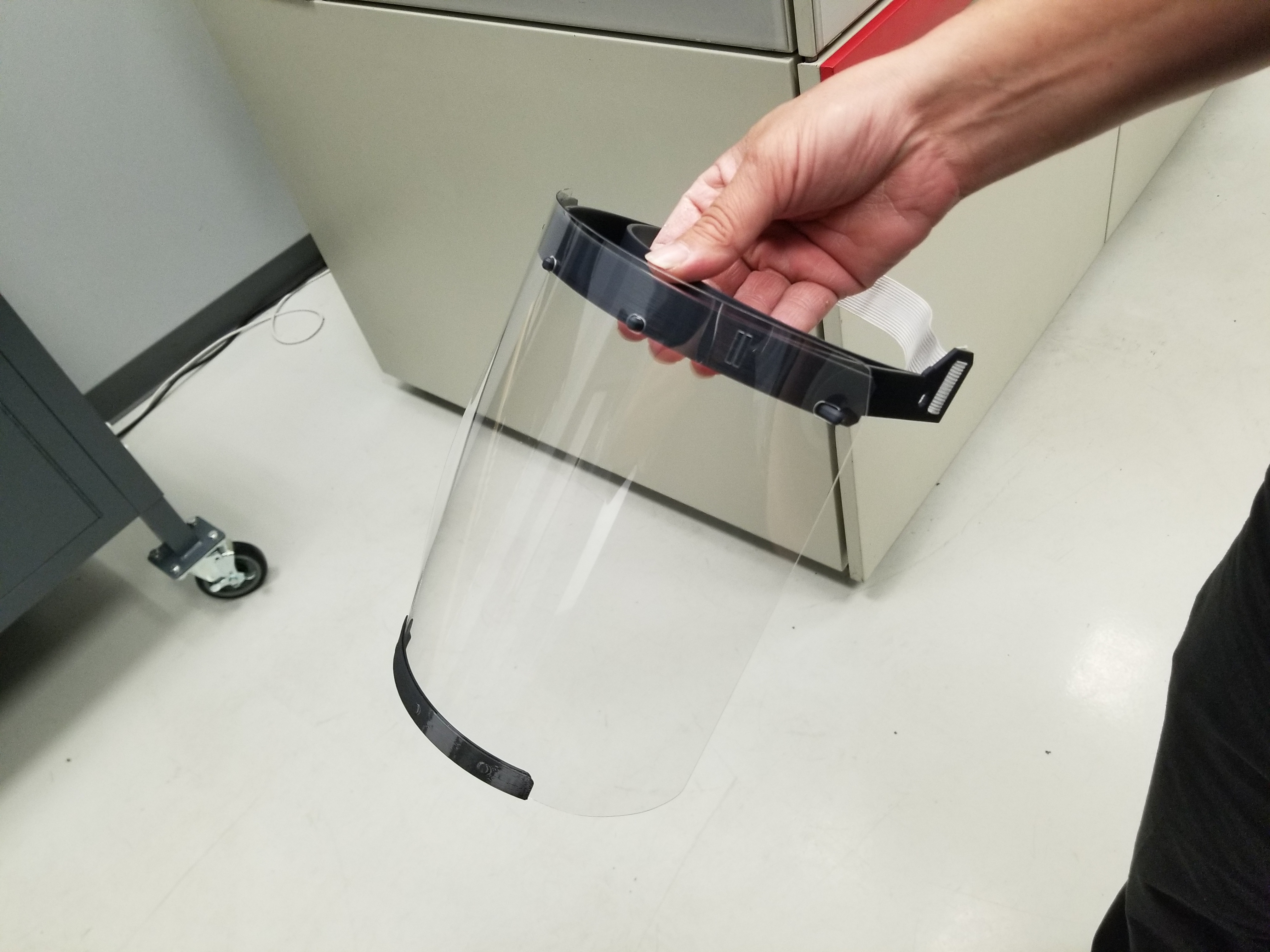
“It is great that we are able to help,” said Merriman, an engineering manager who normally splits time between component design and overseeing production activities. “My father-in-law is a physician and he’s been using a N95 mask a week at a time. What we’re making is intended to protect those masks, and it makes you feel good that somebody might be able to benefit from what we’re doing.”
Dr. Joshua Patt, who works with the orthopaedic surgery team at Atrium Health, said the current shortage of N95 facemasks has forced healthcare workers to use equipment for as long as possible. Another layer of protection is a clear face shield, which allows staff to see multiple patients while re-using N95 masks. The head gear is made of dense non-porous plastic and the shields of PETG clear plastic, which can be cleaned and sanitized between procedures.
“We can re-use them,” Patt said of the shields. “Until they get cracked or scratched or to a point where they can’t be cleaned, we are able to keep going. They protect our patients and they protect the medical staff.”
The process for developing the improvised PPE has evolved rapidly since March 23 when Wall, Hendrick Motorsports’ engineering director, was asked if the organization could use its design and manufacturing resources to produce the face protection.
Patt, who is friends with Hendrick Motorsports president Marshall Carlson, left an example of the face shields on Carlson’s doorstep safely wrapped in a plastic bag. The ball started rolling quickly from there, and Patt said the Hendrick Motorsports team had a prototype produced within hours and multiple alternate versions ready in a few days.
Wall said it was the least the organization could do to give back and added that Rick Hendrick, the owner of Hendrick Motorsports, championed the idea.
“Mr. Hendrick is the biggest cheerleader and the one up front making it happen,” Wall said. “Hendrick Motorsports has purchased the plastic for the machines and for the laser cutting. We’re donating Tad and Mike’s time and experience. Siemens is our technical partner, and their NX software was used for the CAD modeling. We also used the Microsoft Teams platform for communication and collaboration. We had a lot of support.”
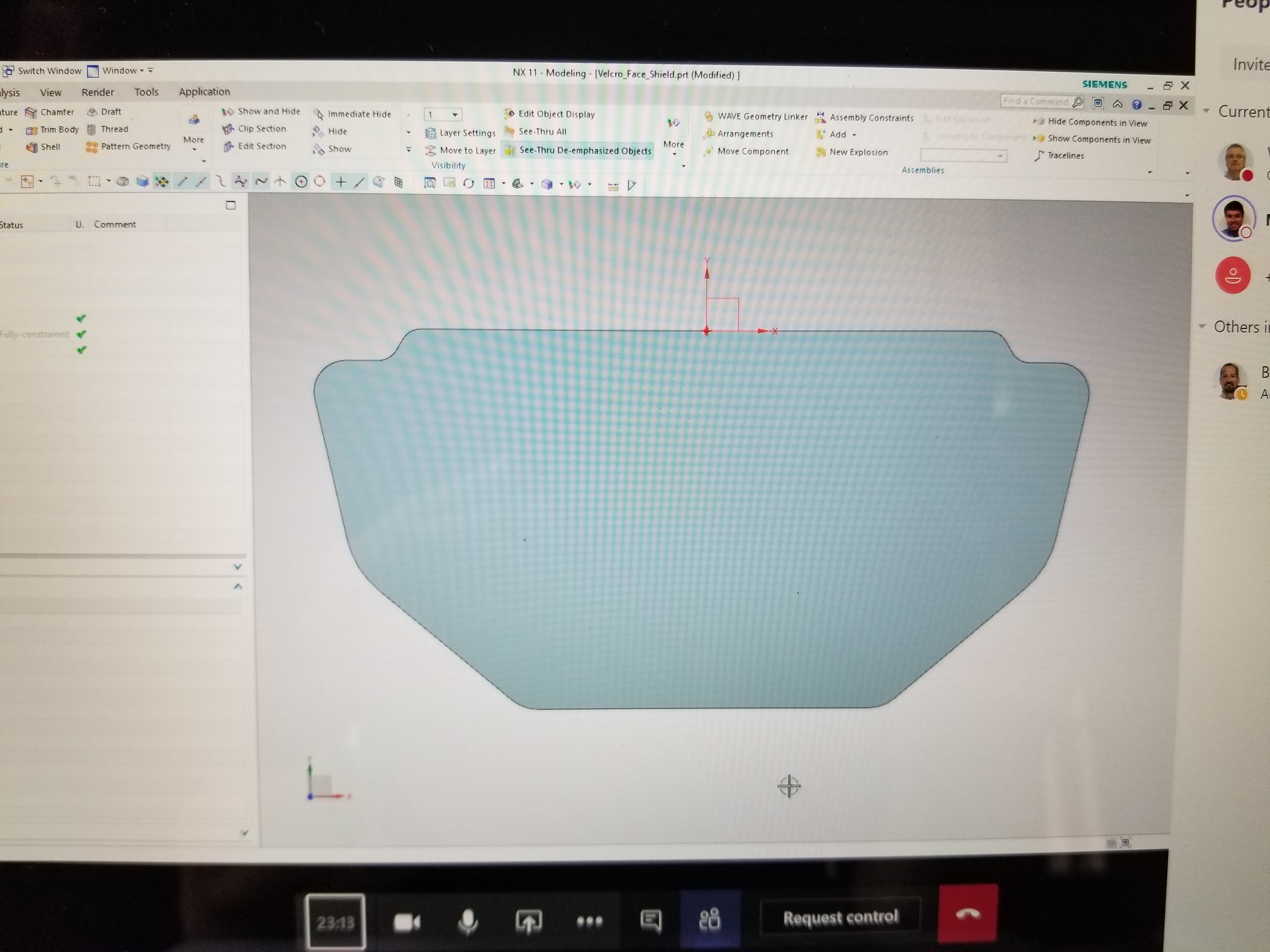
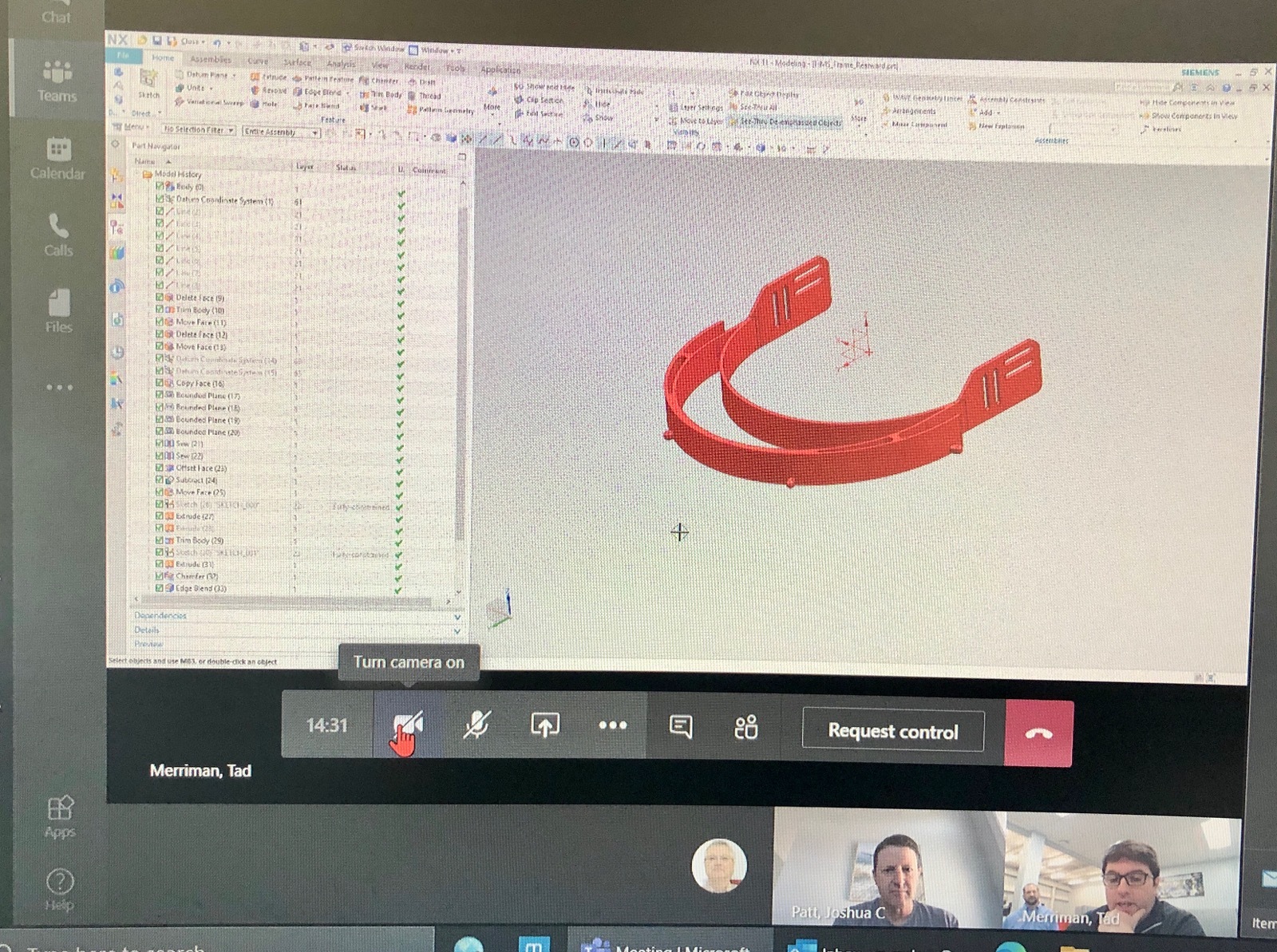
Patt said the gear had to be modified to allow the shield to cover not just the face but the neck area as well. It also must be comfortable enough for the healthcare workers to wear for hours at a time and include a vent so it doesn’t fog up – much like a racing helmet.
“It’s twofold,” Patt said. “Studies have shown high concentrations of the virus in bodily fluids and the work we do in the operating room is prone to splash exposures. That’s why we need this full protection. The way we have it designed now, if you’re in a normal work position with your head tilted down at 45 degrees to see what you’re working on, you should have complete coverage. That’s our hope with this design and those are the little modifications that we’ve been making with the Hendrick Motorsports team.”
Patt added that he hopes the improvised PPE will lead to a long-term design that’s not only economical but will better protect the healthcare workers who use them.
“We don’t know what the next disease is going to be,” he said. “We should be doing our best to provide protection.”
As of April 16, 148 improvised PPE kits have been delivered to Atrium Health. Hendrick Motorsports is making 16 kits per day, which are sterilized before they’re bagged and shipped. Patt is helping coordinate the distribution of the shields, which were first shared with the orthopaedic teams from Atrium Health Orthopaedics and OrthoCarolina who together are providing the urgent and emergent orthopaedic care at the Level 1 Trauma Center at Atrium Health Carolinas Medical Center.
“We dip the parts in 99% isopropyl alcohol, and then all of that gets directly bagged,” Merriman said. “Then we spray the bag down with a disinfectant.”
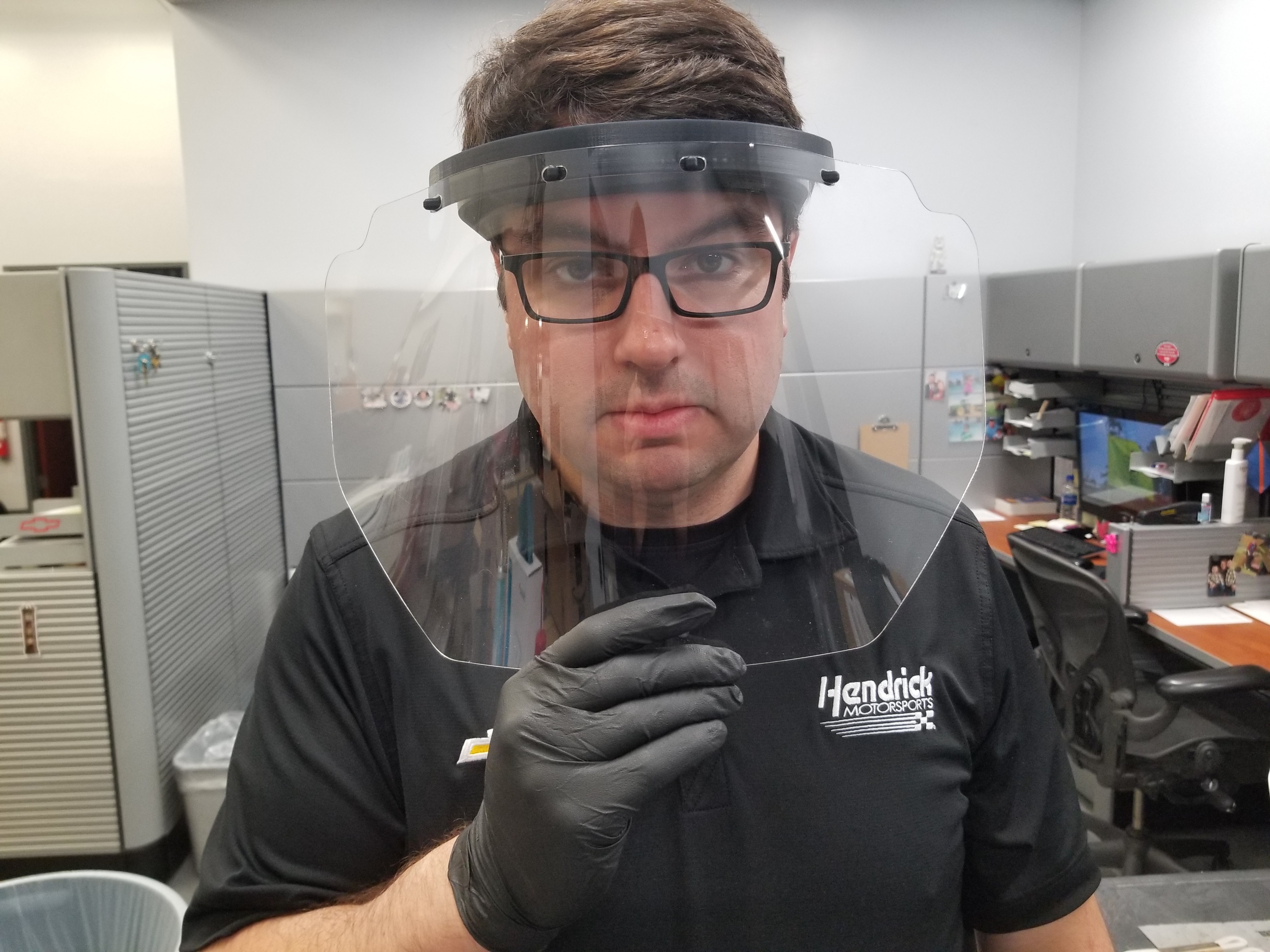
Broskin, an additive manufacturing engineer who develops components for Hendrick Motorsports’ engines, noted that the project feels personal because he knows the improvised PPE will be placed on someone’s head – not on a race car.
“Most of my engineer friends design and build things to make the world a better place,” he said. “In motor sports, we dedicate our careers to making cars go fast so it feels great to do something that may save lives.”
Merriman believes the engineering mindset helps the team maintain a familiar production flow, even though the pieces are different than what they typically work with.
“On the surface, it’s just parts,” he said. “Making parts is what we do. But it changes a little bit when you sterilize them and put them in a bag and you realize, ‘That’s going to someone who’s on the front lines of this crisis.’ That really changes the perspective on what we are doing.”
For Patt, he’s simply grateful for any help the healthcare industry can get as the pandemic continues to stretch its workers and supplies thin. He said the medical staff loves the new shields and that Atrium will soon begin to distribute them outside the orthopaedic teams in the operating room.
To recognize Wall and the rest of the group, Patt said the improvised PPE was named the “RW3” in honor of Wall’s father, Robert, who was the long-time CEO of Cabarrus Memorial Hospital, now Atrium Health Cabarrus.
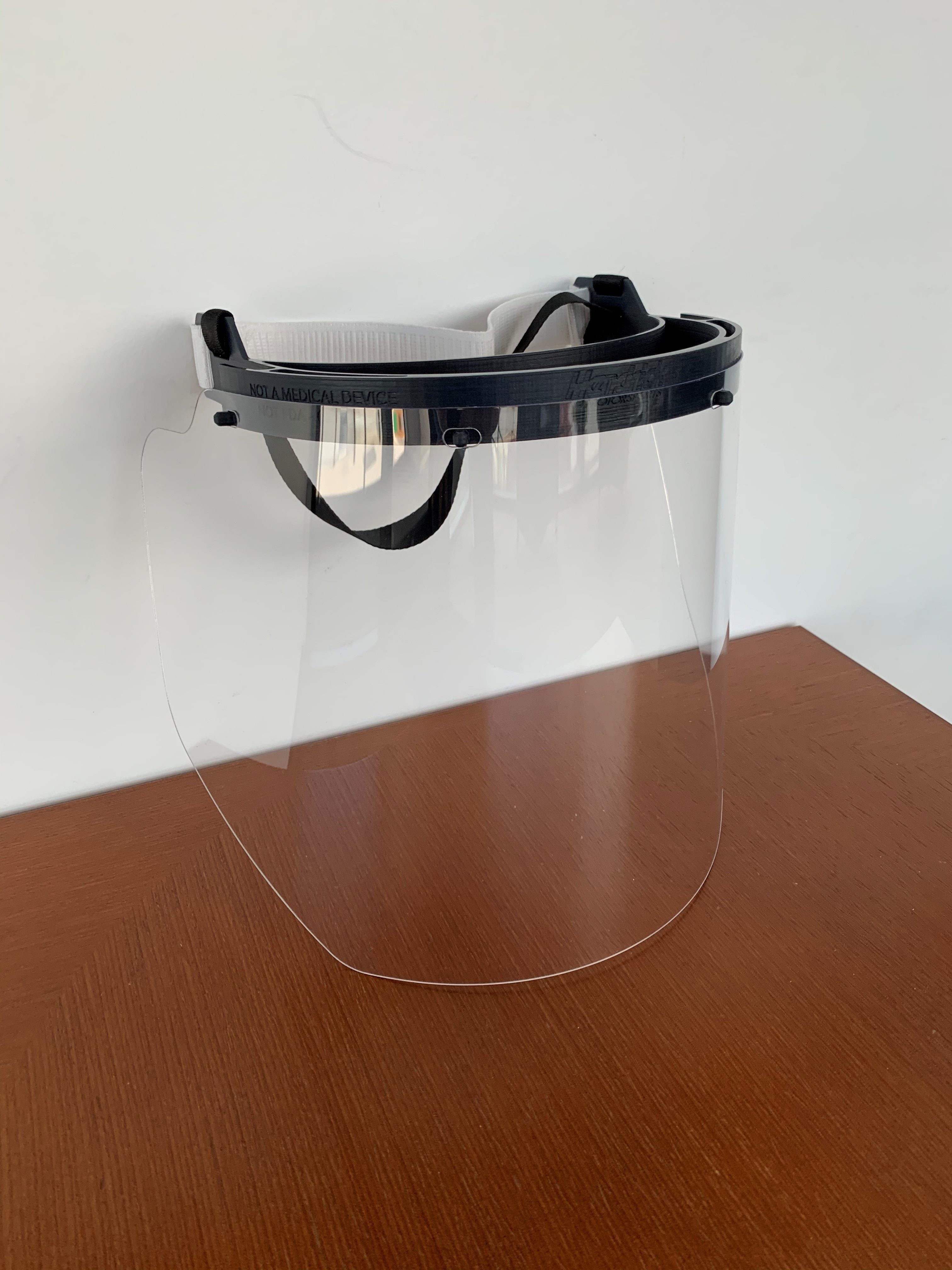
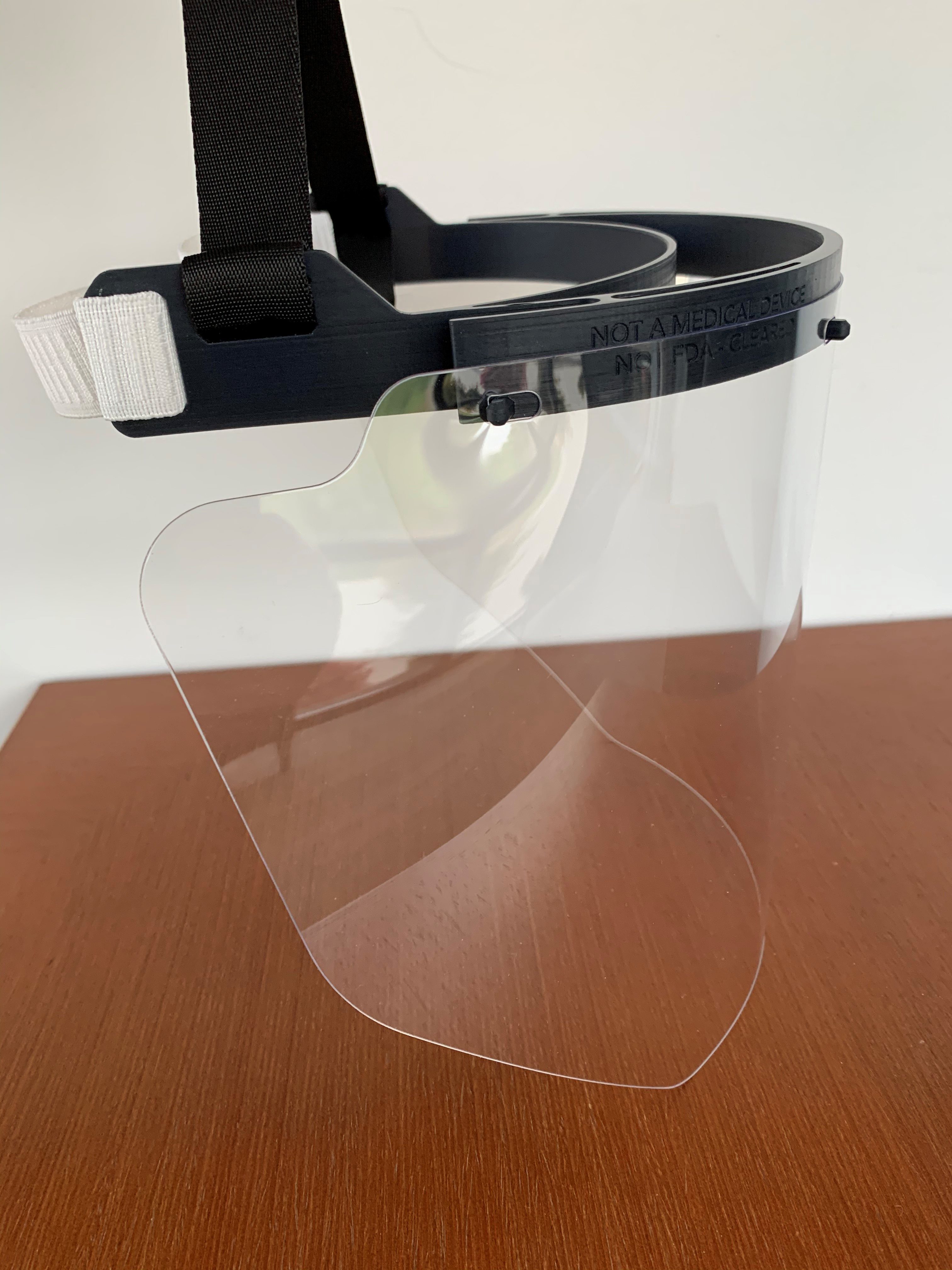
“Being somebody who is on the ground and in the hospital, I just saw a need and communicated that need to my friends at Hendrick Motorsports,” Patt said. “Jim and the engineering team took what we handed them as an idea for a potential plan and, literally, within hours we were on the phone discussing it. We saw a prototype the next day and moved on quickly to improved versions.
“I don’t know how you could possibly look for more support for our medical community. A bunch of people who have never made medical equipment in their lives are improving on our safety within 48 hours of first touching something. It’s pretty amazing and incredibly supportive of our community and our hospital system.”
Carlson, who serves on the Atrium Health board, said he is extremely proud of Wall’s group and grateful for the contributions of the medical community during the crisis. He also noted that Hendrick Motorsports is part of a larger effort from the racing industry.
“Jim, Tad, Mike and the rest of the team are helping in an important way,” Carlson said. “It’s impressive that they’ve been able to shift their focus so quickly from making our race cars go faster to developing improvised PPE that are keeping people safe and healthy. They deserve so much credit for their work.
“Other race teams and NASCAR itself, through its R&D Center in Concord, are making similar efforts to support our medical community with supplies and equipment. It shows how caring and capable our industry is and makes you proud to be a small part of it.”
When the 2020 NASCAR schedule resumes, Carlson already knows who should receive the credit.
“The real heroes are the folks on the front lines,” he said. “Our healthcare workers are making unbelievable sacrifices to keep us healthy and to save lives.
“When we’re able to safely go back to racing, we’ll have them to thank for it – and so much more.”