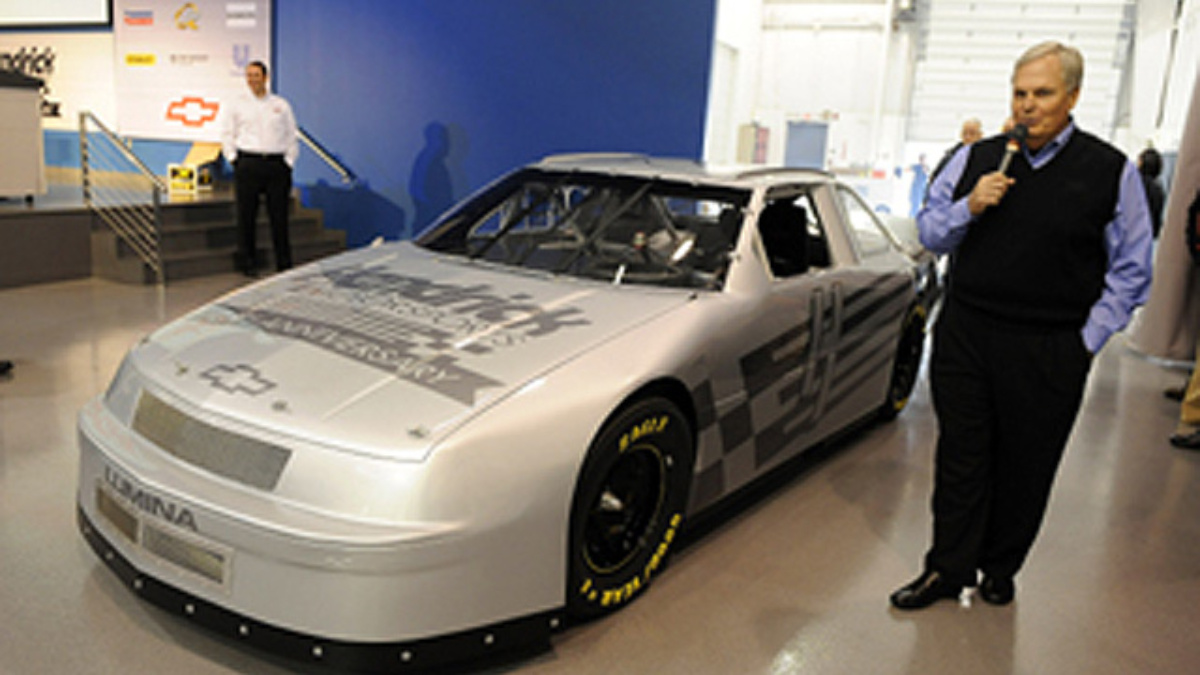
Hendrick presented with first chassis 'Dusty'
CONCORD, N.C. (Jan. 22, 2009) -- Before “Blacker,” the most successful car in Hendrick Motorsports history, and before “T-Rex,” the Chevrolet that prompted NASCAR’s sanctioning body to rewrite its chassis rules:
There was Dusty.
The Chevrolet Lumina was an original, integral piece in the chassis-building history of Hendrick Motorsports. But the rustic car is more than a footnote in the company annals. It represents the innovative approach and optimistic spirit that team owner Rick Hendrick still infuses into his employees.
To commemorate the organization’s 25th anniversary, the restored Dusty was presented to Hendrick at the company’s season kickoff luncheon on Jan. 20. The car was painted silver and bears the single letter “H” in lieu of a number on the side. A small metal plate stamped with “HMS 001 Dusty” sits on the crossbar that goes through the passenger seat.
Building block
When Dusty first was built in 1989, it didn’t have a chassis number anywhere on it. The precise craftsmanship served as the signature mark on Hendrick Motorsports’ initial stab at car building. Under the direction of Gary Dehart, the Lumina -- originally identified as “HMS 89-1 test” -- was to be used for testing purposes.
Dusty made its debut at Talladega (Ala.) Superspeedway on May 6, 1990, with Greg Sacks behind the wheel of the No. 18 Ultra Slim Fast Lumina. Sacks, in his third race for Hendrick Motorsports, climbed from his 17th starting spot to lead 41 laps and finish second behind the late Dale Earnhardt Sr.
Earnhardt, impressed by the car that put up such a fight on the superspeedway, approached Dehart afterward and inquired about Dusty.
“He asked, ‘What would it take to get one of these cars?’” Dehart recalled. “I said, ‘You’ve got to talk to the bossman about that.’”
Dusty secured a pole position -- the first of Sacks’ Cup career -- two months later at Daytona (Fla.) International Speedway. At 195.533 mph, it bested the cars driven by Mark Martin and Earnhardt, who started second and third, respectively.
The success of Dusty -- a runner-up finish and a pole position -- boosted the credibility of the organization’s infant chassis-building program, which enjoyed support from General Motors. The Hendrick crew chiefs initially were skeptical of trading their beloved Laughlin chassis for something homemade. But they welcomed the fact that building their own cars allowed them more freedom, particularly given that NASCAR’s rulebook on chassis construction was relatively thin. A tweak here and an adjustment there often translated into improved handling and speed.
By 1992, Ricky Rudd won the first race in a Hendrick-built car -- known as “Midnight” -- at Dover (Del.) International Speedway. By 1993, all of Rick Hendrick’s teams were running in-house chassis.
“There was no question in my mind that it was going to happen,” said Frank Edwards, an original employee at Hendrick Motorsports. “But at that time we were running Laughlin cars. Richard Broome had come up as crew chief (then on the No. 25 Chevrolet) and was a strict Laughlin man.
“But when Rick Hendrick told me we were going to start a racing team, I quit what I was doing and moved 170 miles to go to work for him. So when he makes a statement that he’s going to do something, there wasn’t any question in my mind. There were going to be Hendrick in-house cars.”
Dusty was the first, and the chassis builders got some quality time with the car thanks to its driver.
“When I got here, I helped rebuild it a bunch of times,” said Mark Whitten, who started his career at Hendrick Motorsports working for Dehart. “It seemed like Greg Sacks wrecked it every time out. He was fast, but he wrecked a lot. It was great when he would go out there and sit on the pole or go to a test at Charlotte and be the best out there. But it was comical that it would wreck almost every time out.
“Somebody would call over and say, ‘We need another car.’ Sacks was unbelievable. He was not scared of anything.”
Dusty, which was named after an avid NASCAR fan, was used by various drivers, like Sacks and Rudd, during its three-year stint with Hendrick Motorsports. It didn’t win a race, but the unassuming, flat-gray chassis triggered theories that were perfected during testing and then applied en route to Hendrick’s championship runs in 1995, 1997 and 1998 with Jeff Gordon and 1996 with Terry Labonte.
“I don’t know if it ever won a race,” Dehart said of Dusty. “But it contributed to everything we built afterward.”
Play day
“Put on new tires, and take off that restrictor plate.”
Hendrick’s instructions made Dehart’s stomach drop.
Dehart and his group had just loaded up Dusty from one of the company’s “play days” in November 1991. Hendrick was known to host events for sponsors to experience driving or riding in a race car, and restrictor plates would be put on the cars for safety reasons.
Dehart knew that Hendrick, a true racer, wouldn’t want any part of that. That’s why he breathed a sigh of relief when his group had Dusty loaded up. But Hendrick showed up in the nick of time, and Dehart could only say, “Yes, sir” when asked. The restrictor plate was coming off.
“He made some pretty impressive laps in it,” Dehart recalled. “Of course, Rick’s a race car driver. He’s got that natural knack at driving. He impressed all the people who drove the car, even the drivers.”
And then he hit the wall.
Dusty was sent back to the body shop for repair. Notes taken on the chassis state: “Wreck by Rick -- Nov. 20, 1991 -- needs front and rear clip.”
Dusty stayed in circulation at Hendrick Motorsports until 1992, when it was sold. It didn’t resurface -- except for the occasional storytelling opportunity -- until 2005, when ARCA driver Bobby Gerhart told company general manager Marshall Carlson he thought he had Hendrick’s first chassis.
Hello, hot rod
The car really hadn’t meant that much to Gerhart when he purchased it in 1997 from an ARCA team that was shutting down in Indiana. The seller mentioned that it was Hendrick’s first chassis, but Gerhart didn’t give it much thought until his ARCA team was testing at Daytona in 1998. He had a brand new speedway car built for the occasion, and it wasn’t doing the job. So Gerhart climbed into the chassis called Dusty.
Everything felt right, and for the first time that day, Gerhart wasn’t distracted by issues with the car. It seemed to do most of the work, and he could focus completely on driving.
“I don’t care how fast it is,” Gerhart recalled radioing to his team. “We have to make this car fast. It drives so much like a car should. This is going to be my hot rod.”
Dusty helped Gerhart establish a reputation as an excellent superspeedway racer. He earned his first ARCA win in the car -- a Daytona victory in 1999 -- and went on to win three more times at the historic racetrack.
“To this day, that was my best speedway car,” Gerhart said. “It should have won the race in Daytona in 1998. But it won in 1999 and finished second in 2000. It began to help me put the ingredients together to have a real superspeedway program. It all started with a car of that caliber.”
From building block to learning tool
Dusty affected whoever got behind the wheel of the Chevrolet, but it had the same impact on those who helped restore it for Hendrick. Restoring Dusty was an idea that Carlson had three years ago when he learned that Gerhart owned the Chevrolet, which at that point had been reformatted for ARCA racing.
“It’s a significant part of our history, and we were able to present it at a significant moment in time for us,” Carlson said. “What’s really neat is all the folks that have been involved made time and effort and put their energy into putting this car together for Rick.
“Everyone really was passionate about putting their mark on it.”
Michael Myrick, another longtime Hendrick Motorsports employee, Dehart and Edwards inspected the car and verified it was Dusty. The Chevrolet showed the scars from more than 15 years of NASCAR and ARCA racing. But there was no mistaking the chassis. This was Dusty.
Only this time, instead of being a pioneering adventure, Dusty was a learning tool. New employees assigned to work on the car picked the brains of veterans like Whitten and body shop manager Ron Reedy who were around during the early 90s. A common question -- “Why did you do it like this?” -- often elicited a standard response: “It was the only way we knew how.”
“Well, that was the best way we knew how back then,” said Whitten, who now oversees Hendrick Motorsports’ chassis-building operation. “For instance, the roll cage. We had to go completely through the frame wells, and it was welded on top and welded on the bottom. It made it strong as it could be, but it doesn’t need to be that strong, and that’s something that made it heavy.”
Frame rails today are an eighth of an inch in thickness, whereas during Dusty’s era, they were 3/16th of an inch. Thickness, chassis builders learned, made the car durable, but it didn’t necessarily translate to success on the racetrack.
“It was crazy heavy and stiff,” Whitten said. “Now you try to make it stiff but with other ways -- not just adding thicker wall tubes and stuff like that.”
The bodies were made of the same sheet metal that manufacturers used on passenger cars. The zinc coating had to be removed for every weld, Reedy recalled. And every Lumina had the assembly line touches -- like an etching for the radio antennae.
The inadvertent history lesson provided younger Hendrick Motorsports employees with an appreciation for the way things were and the veterans with a longing to return to that time. Today, the NASCAR rulebook is substantially thicker on chassis and body construction.
“In the old days, it was more fun,” Whitten said. “The box you worked in was bigger. You could mess with more stuff; you could come up with ideas. Now it’s getting real hard to come up with ideas. There are so many numbers that NASCAR makes you have that made this box so much smaller trying to keep everybody equal that it takes some of the fun out of it.”
Dusty also was a bit of a conversation piece, and the veterans shared their stories with each other and the newcomers. Whitten recalled how heavy the chassis was, but also the crazy hours that his department would work to fix the latest damage or build another car. He remembered Dehart’s perfectionism and his insistence that his employees share the same devotion to detail.
Folks like Myrick took the opportunity to sit back and soak it all in.
“The best thing has been listening to Frank, talking to Ron Reedy, seeing Mark Whitten talk to his guys,” Myrick said. “It’s been really neat to hear all those stories because you’ve got so many of those people who were here. They talk about that time when things were maybe a little simpler and performed better in a lot of cases than they do today. It’s been neat seeing those guys reminisce about that stuff.”
Doing it right
Attention to detail was of the utmost importance to anyone who helped restore Dusty.
Whitten and his employees smoothed out the scars Dusty collected during its NASCAR and ARCA life, replacing the front clip, rear clip, some tubing and parts of the firewall.
Jeff Andrews, director of engine operations at Hendrick, had to locate the many engine parts not in stock any more on the company’s shelves. During his search, he discovered that Keith Dorton -- brother of the late engine guru Randy Dorton -- had the Pontiac cylinder heads necessary to rebuild the older and much outdated engine.
Reedy dug up some authentic sheet metal on the Internet that Myrick sent one of his employees to pick up in Miami.
“(The seller) had all the pieces that we really, really needed,” said Reedy, who now heads Hendrick’s body shop. “He even had some glass for the car and the templates.”
Reedy studied the body of the No. 24 Lumina that Jeff Gordon drove to win the inaugural Brickyard 400 at Indianapolis Motor Speedway in 1994. Gordon’s Brickyard Chevy was the second car built for the No. 24 team led by crew chief Ray Evernham.
“We made everything time period correct,” Reedy said. “It’s not actually built as a superspeedway car as it was originally, but it’s built as an intermediate because it has more balanced looking front fenders. I’m really proud of how it came out.”
Everything mattered – from the style of cylinder heads to how the window net was mounted. The attention to detail -- a hand-me-down from Dehart -- also is a reflection on the organization’s leader; a measure of employee gratitude.
“It’s a real tribute to Mr. Hendrick as our leader that everybody wanted to be part of it and wanted to make sure that it looked as good as possible,” Reedy said. “I know everybody feels the same way I do. I wouldn’t be where I am or have the things I have if it weren’t for Mr. Hendrick.
“I think everybody here feels they’re extremely lucky to No. 1 have a job; No. 2 have a job in racing -- that’s not even like the real world. And then No. 3 to have a job in racing with a team like this.
“This is as good as it gets.”